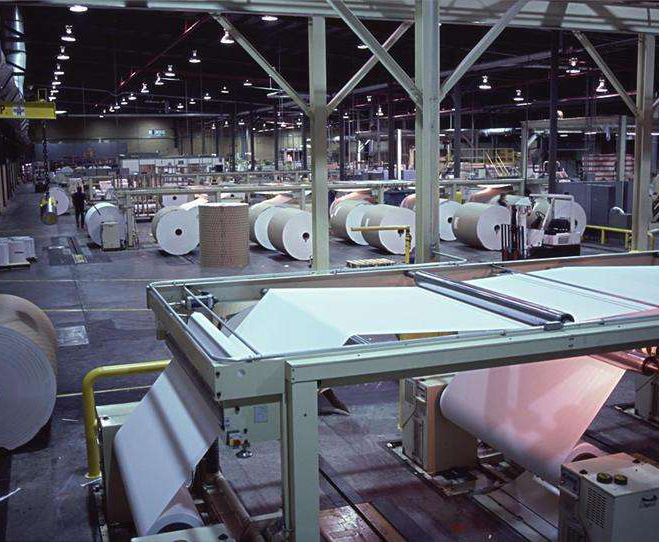
By using a liquid ring vacuum pump, the cost of papermaking can be reduced and the quality of paper can be improved. It is widely used in the vacuum system of the papermaking industry and the field of water removal in paper machines. The application of vacuum pumps in the paper industry includes black liquor evaporation, coarse slurry washing machine, lime slurry and filter, sediment filter, vacuum dewatering machine, raw material and white water degassing system, slurry box compressor, suction tank, pressure roller, suction roller and transfer roller, and vacuum pressing.
Black liquor evaporation
The black liquor evaporator in the pulp mill is used to concentrate the black liquor produced in the pulp cleaning process, so that these liquids can be recovered in the recycling furnace for chemical agents and reused in pulp production.
Coarse pulp washing machine
Before bleaching or other raw material preparation work, the coarse pulp washing machine removes pulp chemicals ("black liquor") from the papermaking raw materials. The coarse slurry washing machine is a typical horizontal drum filter machine. The drum shaped cavity can generate a vacuum. When the drum rotates in the raw material slurry, vacuum can cause the raw material to adhere to the outer surface of the drum and help remove (clean) black liquor from the raw material.
Lime slurry and filter
The lime slurry filter in the pulp mill is used to recover lime during the clarification process of white water. Similar to the coarse slurry washing machine, the lime slurry filter is a typical horizontal drum filter machine. The inside of the drum can generate a vacuum. When the drum rotates in lime slurry, a lime cake is formed on the outer surface of the drum. Then scrape it off and reuse it during the white water process.
Sediment filter
In pulp mills, sediment filters are used to remove non combustible suspended particles, fully burned carbon particles, iron containing compounds, and insoluble furnace body fragments from the "green liquid" before pyrolysis. The sediment filter is a typical horizontal drum filter. The inside of the drum can generate a vacuum to extract particles from the green liquid.
Vacuum dehydrator
A vacuum dehydrator is used to dehydrate raw materials during the preparation stage to increase their concentration. The dewatering machine is a typical horizontal drum filter used to dewater pulp in proportion to increase the concentration of raw materials.
Raw material and white water degassing system
The raw material and white water degassing system is used during the raw material preparation stage to remove air carried by the raw material or air from the dilution water before the raw material enters the mixing tank. The raw material and white water degassing system is very important because it removes air from the papermaking raw materials, which can cause pinholes on the paper and greatly affect the printing quality, mechanical properties, and overall quality.
This degassing system is a typical two-stage vacuum system: the boiling point of the raw material at the inlet of the first stage vacuum pump (27-28 in. HgV), and the inlet pressure compression ratio of the second stage vacuum pump is 4:1. A pre condenser is typically used between the degassing vessel and the primary vacuum pump, and a small inter stage separator is required to be installed between the two vacuum pumps. Vacuum pumps are made of standard materials.
Slurry mixing box compressor/vacuum pump
The slurry box compressor/vacuum pump is used in the "air cushion" slurry box to generate a pressure/vacuum above the level of the raw material in the slurry box (or "raw material pool"), maximizing the control of the raw material discharge speed ("jet" speed). Pumps are typically used as vacuum pumps and compressors through a series of valves, generating vacuum or pressure in the void volume above the "raw material pool" to control the static pressure head of the mixing tank.
Water suction tank
The suction tank is a stationary device that directly dehydrates pulp from the forming section of the paper machine. There are usually 2-10 suction tanks on a paper machine, which are usually connected into a main pipe. Due to the large amount of dehydration, a pre separator needs to be installed between the suction box and the vacuum box. The liquid ring pump is used to generate vacuum in the vacuum box of the suction tank.
Fu Roll
Many times, the roller is the last vacuum point on the forming section, known as the most important dewatering part of the paper machine. When the paper enters the pressing section after leaving the press roller, the dryness of the paper affects the dehydration performance of the pressing section and the steam consumption of the drying section. The roller is stationary and has a rotating porous outer shell. The roller can have 1 or 2 vacuum zones.
Suction roller and transfer roller
The suction roller sucks the paper away from the mesh on the forming stage and guides it into the pressing section. Then, in the pressing section, the transfer rollers transfer the paper from one blanket to another. These processes are not formal dehydration, but can remove a small amount of water from the paper.
Vacuum pressing
Vacuum pressing uses mechanical methods to extract moisture from paper. In the pressing section, rollers with granite and hard rubber surfaces are in close contact, forming a "pressing zone". A typical paper machine may have 1-3 "press zones". When the paper passes through the press zone, the moisture inside is squeezed out and seeps into the press blanket. As the paper passes through the press section, these blankets are used as transportation tools and pads for the paper. During the dehydration process, there are vacuum and non vacuum rollers in the pressing section.
Woolen cloth suction tank
During the pressing process, the pressed fabric (or "wool cloth") contains a mixture of water, chemical materials, papermaking materials, soil and fillers, viscous residues ("asphalt") generated during the papermaking process, and adhesive ("adhesive") produced from recycled paper. Due to each piece of woolen cloth being a continuous cycle, it is necessary to remove moisture and contaminants before the next pressing begins. The vacuum suction tank is a fixed suction box that exceeds the width of the blanket and absorbs water and pollutants accumulated during the pressing process of the blanket. Each piece of woolen cloth has two vacuum suction tanks. When using a vacuum suction tank, it must be pre separated to avoid carrying water into the vacuum pump.
Anti blow box
In the pressing section, there are some "open" pressing zones that do not provide support for the paper before entering the pressing zone. Airflow may cause the paper to shake, fold, or break. The anti blow box is fixed and used to create an upstream vacuum in the pressure zone before the paper enters. Since the anti blow box cloth is used for dehydration, there is no need for pre separation treatment.